How does Low-E Insulation compare?
There are many questions and misunderstandings online about foil insulation, how it works and how foil insulations compare to each other and ‘traditional’ insulation.
This blog will answer some of the most fundamental questions about Low-E Reflective insulation and foil insulation in general.
If you want to know more about Low-E Insulation and how it works, you can read our blog: How does Low-E insulation work?
Foil insulation is a straightforward idea; use pure aluminium to reflect heat back to the heat source. So, why do so many companies get it wrong?
It is possible to reflect heat with a single layer of aluminium; that bit is easy! The problem is when you do that; it creates an increased risk of condensation forming on the product’s surface.
So, the obvious answer is to add an additional separating layer to reduce the risk of condensation and create a thermal break. Different companies have tried to do this in several ways, using various materials and methods. The problem is that the materials and production methods tend to create additional issues that must be dealt with.
Some of the most common questions we get asked are;
- What is the difference between Low-E Reflective Insulation and other ‘foil’ Insulations?
- What is the difference between Aluminium and Mylar?
- How is Low-E Reflective Insulation different to traditional insulation?
Other types of ‘foil’ insulations
Single-Layer Foil Insulation
What is Single-layer foil insulation?
Single-layer foil insulation consists of a single layer of reflective foil. This foil is often made from aluminium and is designed to reflect radiant heat rather than absorb or transfer it.
Bubble Wrap Insulation
What is bubble wrap insulation?
Bubble wrap insulation consists of a layer of air bubbles (usually made of polyethylene) sandwiched between two layers of reflective foil.
The air in the bubbles provides a barrier against heat loss, while the foil reflects radiant heat.
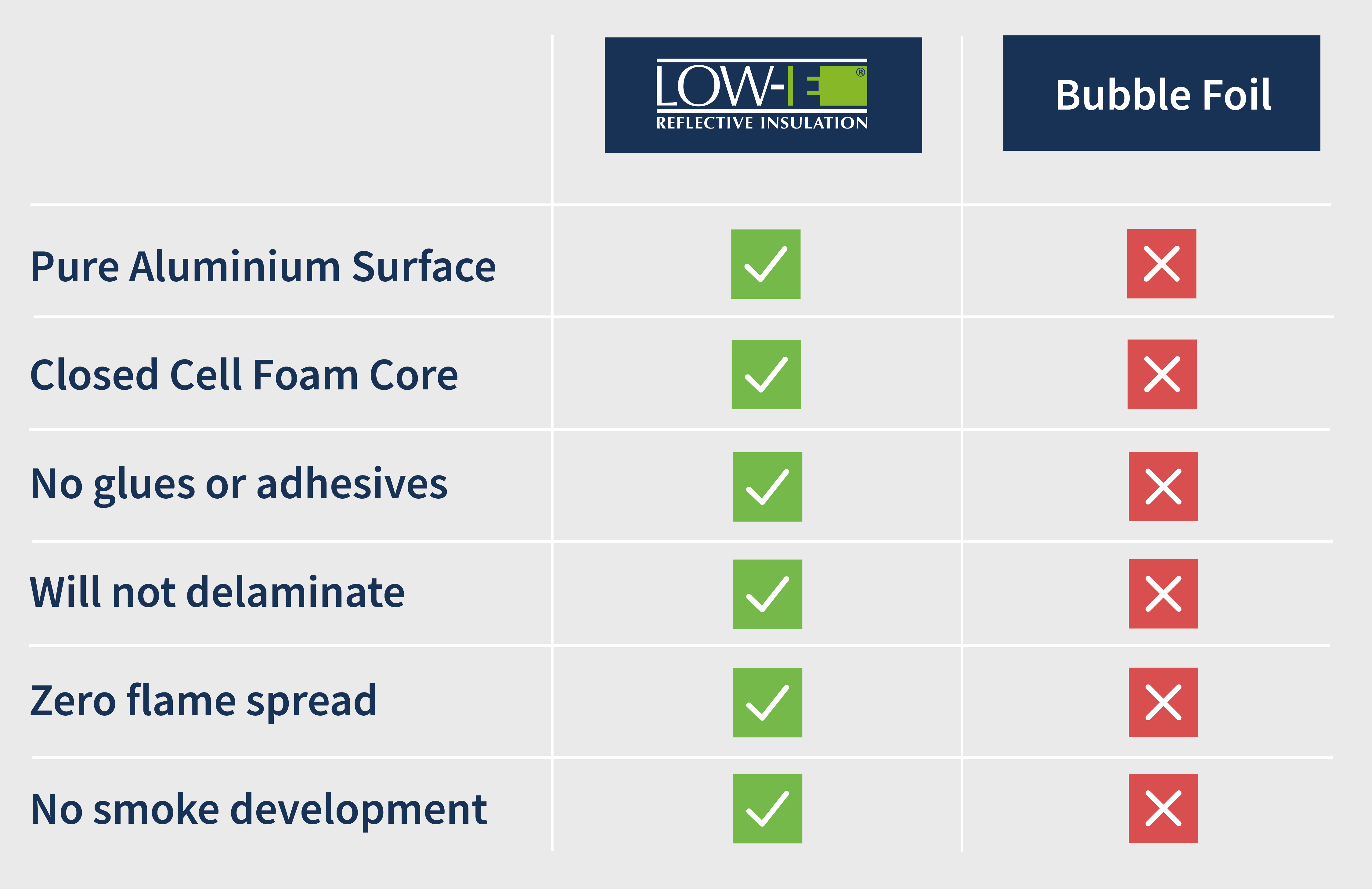
Problems With Bubble Wraps and Single Layers
Bubble Wraps and Single layered products have an increased risk of condensation forming on or in the product.
Glued and laminated products contribute to fire spread; the glues break down over time, and the products delaminate, especially when subjected to heat and cold, the way insulation is.
The obvious problem with a fibrous material is that it can absorb moisture. However, products with fibrous cores usually have multiple layers and are usually referred to as Multi-Foil Insulations, and these can have a whole host of problems.
Aluminium is an electrical conductor. Please use caution when working around electrical sources, including overhead power lines.
Low-E should be stored in its bag on a flat, dry surface, out of direct sunlight, until it is ready for installation.
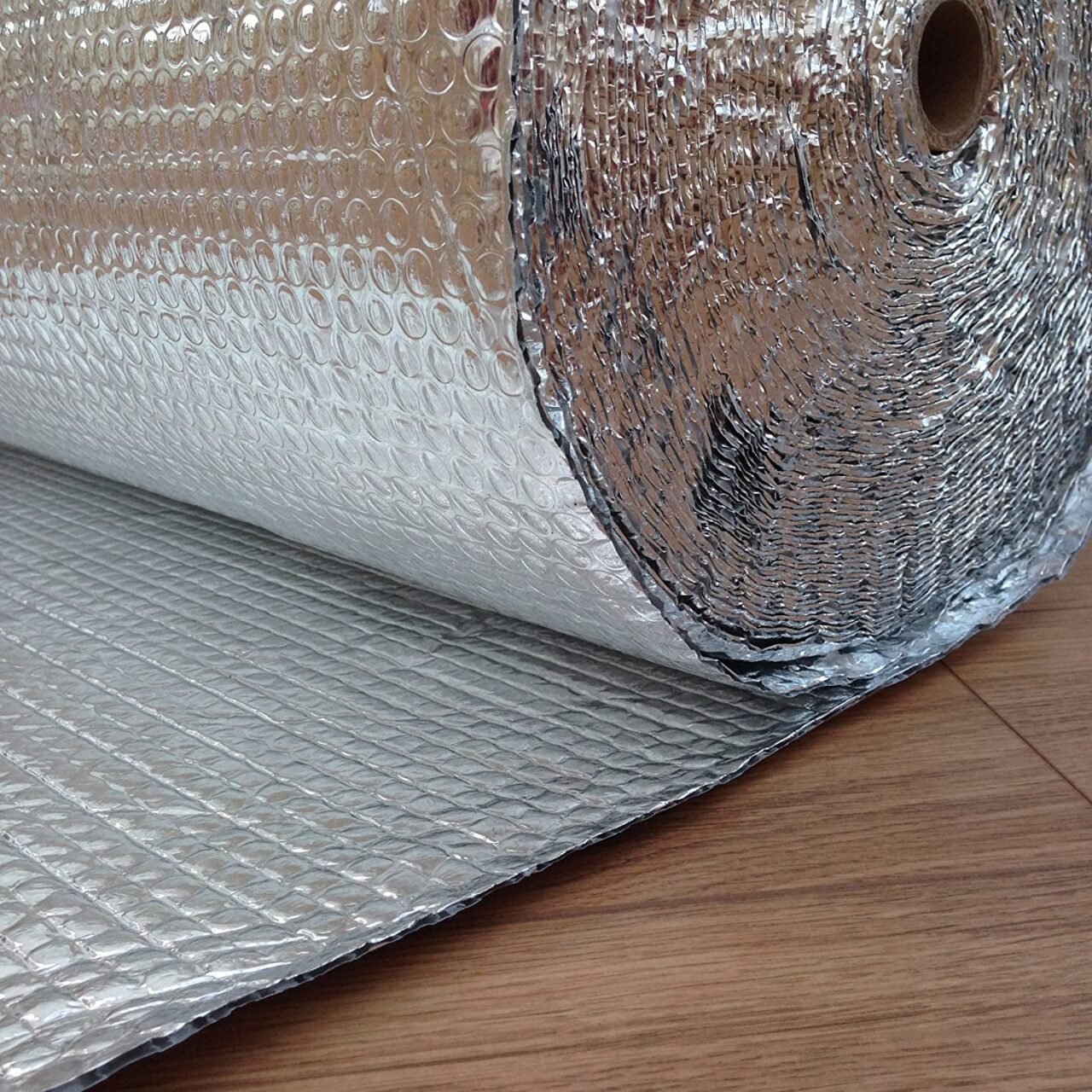
Multi Foil Insulation
Multi-foil insulation is a multi-layered product that often has lots (and lots, and lots) of layers, which tends to make them thick and heavy, which (in our opinion) defeats the purpose of thin reflective insulation. These multiple layers of thin foil are separated with other materials like foam or wadding.
It also makes them hard to work with, but the problems don’t end there.
Multi-foil products tend to be made from synthetic materials, resulting in both the production and disposal processes having negative environmental impacts.
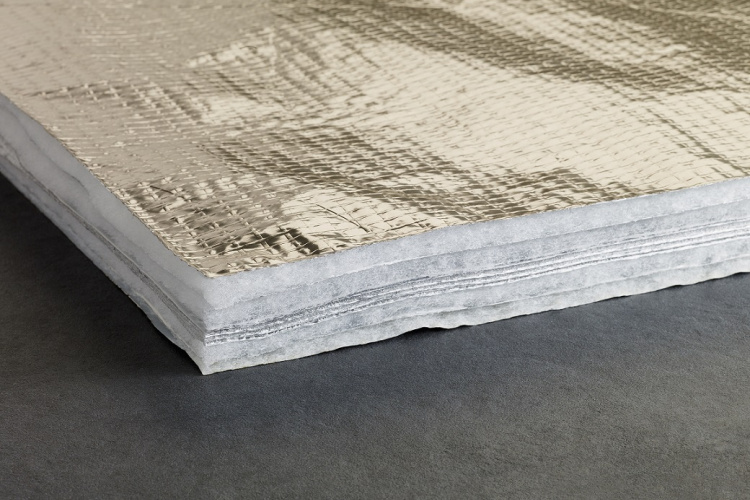
What is the difference between Low-E Reflective Insulation and other ‘foil’ Insulations?
Most foil insulations on the market tend to have poor fire ratings or no fire testing, which means they are unsuitable for use in a wide range of applications. These products need to be installed behind the plasterboard to comply with fire regulations. But that is little help if a fire starts in the wall cavity.
Poor fire ratings
Multi-foil insulations are not used or found in countries where regulations and foil insulation are widely understood. In the USA, for example, foil insulation has been used for over 30 years, but multi-foil insulation is not sold there and cannot be used due to its lack of compliance and failure to meet basic Fire Safety Standards.
Fibrous Cores
Any product with a fibrous core risks moisture absorption. When that product has a layer of aluminium (or Mylar) as an outer layer, you risk the moisture travelling through the core of the product, the product sweating, and, over time, corroding and delaminating.
Thick and Bulky
Some of these multi-foil products have more than 15 layers. and can measure anything from 35mm to 75mm thick, ultimately defeating the idea of a thin, efficient reflective insulation.
Companies making these products are making bulk insulation because they are using Mylar and don’t understand foil insulation, so they are trying to be all things to all people.
Hard to install
Anyone who has handled multi-foil insulation will know their multiple layers make them heavy, difficult to cut, and even harder to work with. They are very labour-intensive (and therefore expensive) to install.
Dragging on Screws
If you have tried to install multi-foil insulation, you will know that their multiple layers and fibrous cores tend to catch on screws, causing them to “bag up”, causing the multi-foil to rip and tear, again costing you time and money!
Larger Battens Needed
These thick and bulky multi-foil products require thicker battens, longer screws and fixings, but a lot of multi-foil insulation companies tell customers their products can be installed using 20mm or 25mm battens.
The problem is multi-foil products can be anything from 35mm to 75mm thick. Manufacturers fail to explain that creating a 20mm airspace beside a product would require a minimum 47mm to 97mm batten (as long as you also maintain an airspace above the insulation).
Do not meet claimed u-values
If any foil insulation is installed with a smaller counter batten than required and has no airspace beside the foil surface, it will not achieve the claimed (or required) U-value for that application.
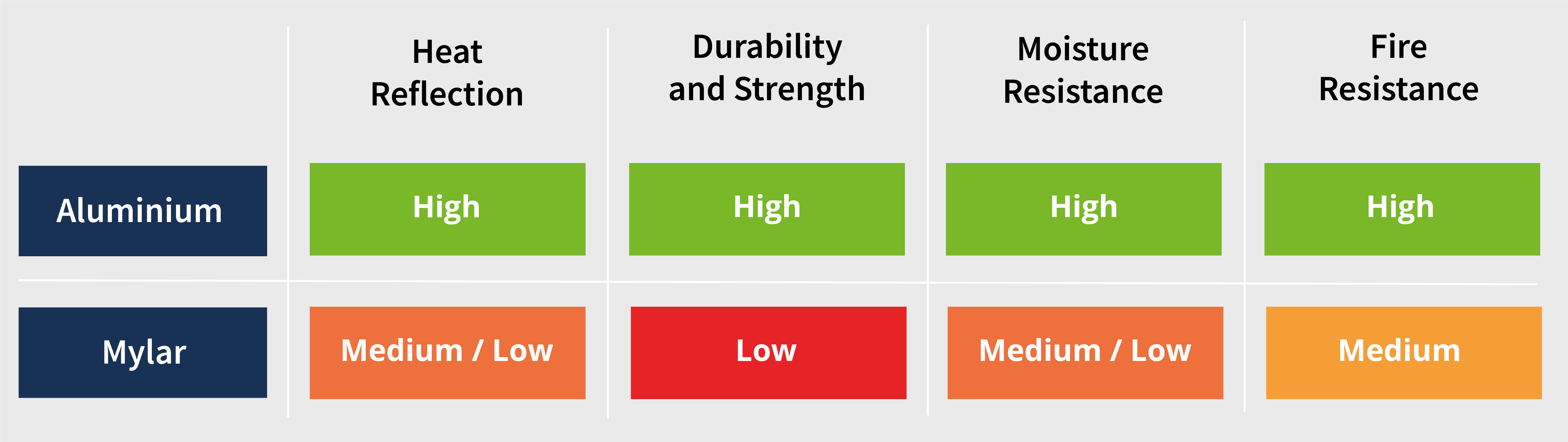
What is the difference between Aluminium and Mylar?
It’s important to understand the difference between Aluminium and Mylar because they look very similar. Although Mylar has some reflective properties, it is far from the same quality as products solely made of aluminium. So why should you avoid products that use Mylar instead of Aluminium?
What is Mylar?
Many ‘foil’ insulation products are made from a product called Mylar instead of aluminium. Only aluminium has a naturally low emissivity value. Mylar is much cheaper to produce. It is plastic that has been either laminated or painted with an aluminium coating.
Companies that use Mylar claim it to be a low-emissivity product. But Mylar, while it looks ‘shiny’ and is good at reflecting light, it does not reflect heat in the same way as aluminium.
You tend to see Mylar used in a lot of single-use applications. (Emergency foil blankets, packets of crisps and Kit-Kats wrappers). It might be good at keeping food fresh, but it is not something you want to use as part of an insulation material.
These coated plastics crack, chip, peel, and delaminate within a very short space of time (especially when exposed to heat and cold, as often as insulation is).
You end up with the emissivity value of plastic rather than aluminium.
Here, you can compare Low-E Insulation and several other foil insulations on sale today.
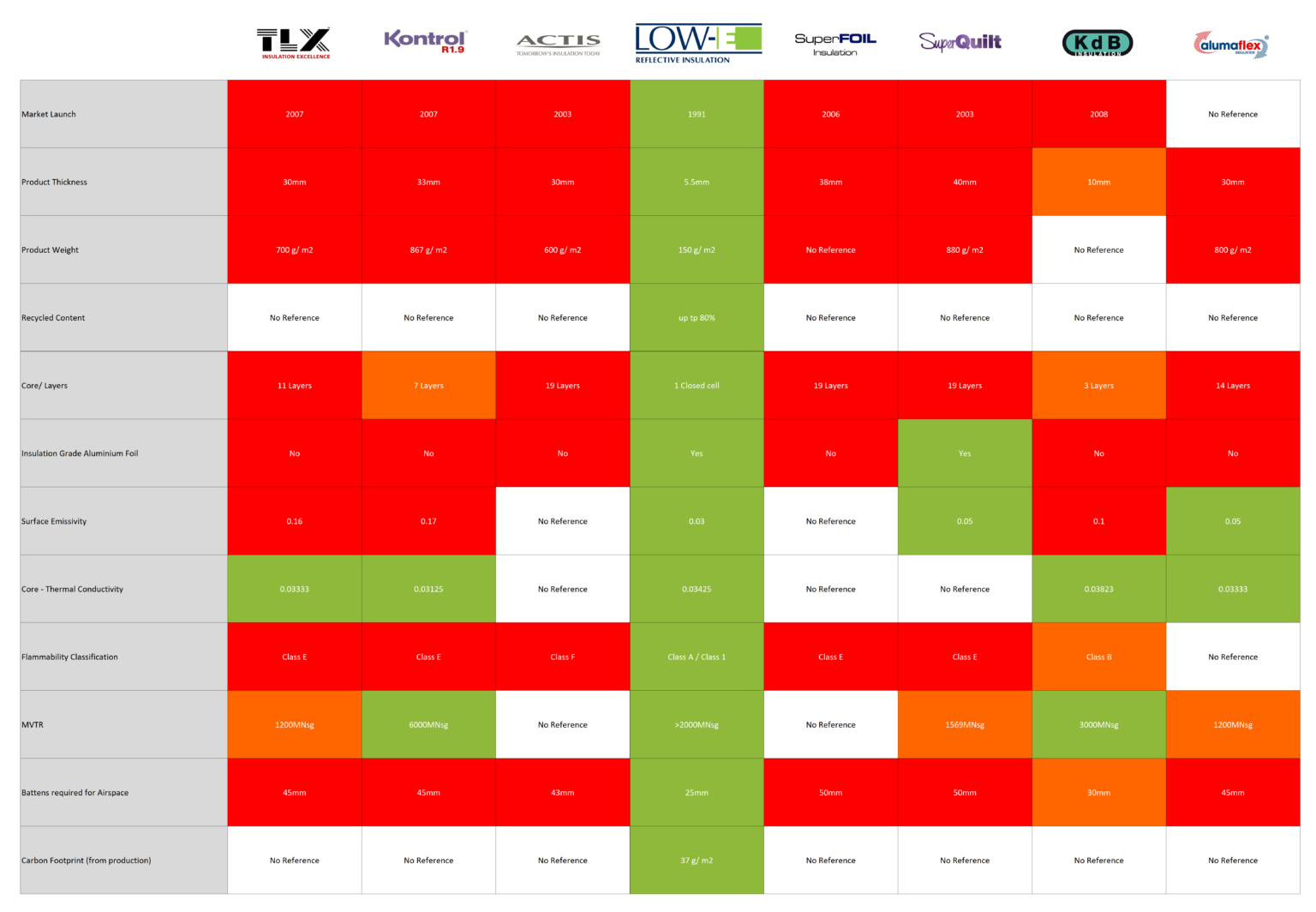
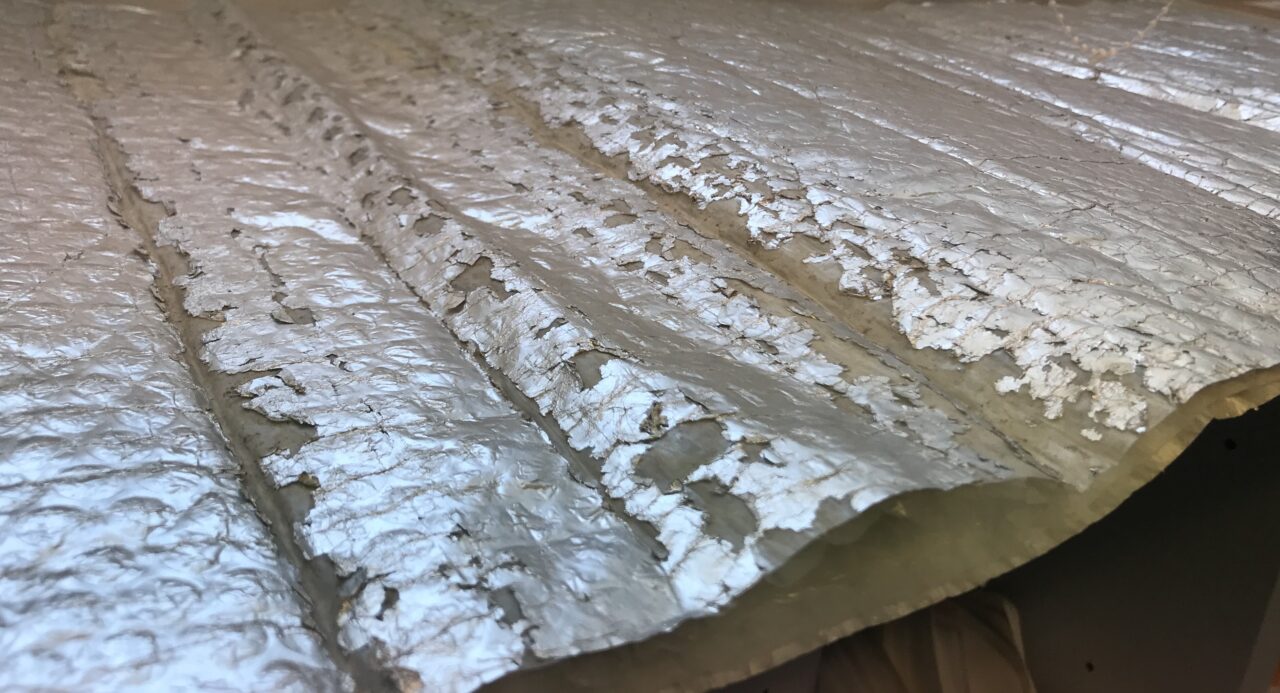
How is Low-E different to traditional insulation?
Reflective insulation is not a new idea and is not supposed to replace all other insulation materials.
Low-E is designed to complement an insulation system and to address issues not solved by traditional insulation, such as:
- Radiant heat
- Air-tightness
- Moisture control
For years, people have thought that to insulate better, they should simply add more and more material, believing that the thicker the insulation, the better it works.
However, more is needed to solve the problem. Very high R-values don’t stop heat transfer; they only slow it down. You cannot ignore the need for good U-values, but by addressing the U-values alone, a large percentage of heat transfer is being ignored.
All insulation materials have drawbacks, so using more and more of the same material may only compound a problem.
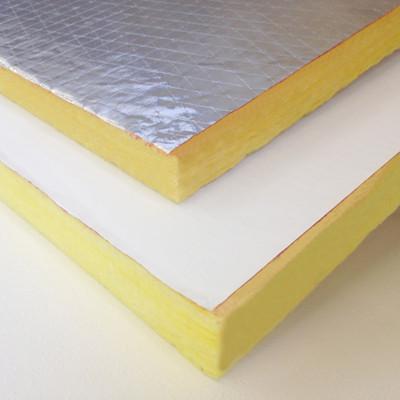
Fibrous Insulation
Fibrous insulation materials are made from tiny fibres that can be natural or synthetic. It works by trapping air within its fibres, which reduces heat transfer by convection and conduction. It relies on restricting airflow and being made out of a material that is naturally a poor conductor of heat. So naturally, the denser and thicker the insulation is, the better it is at preventing heat and sound from travelling through is and being lost from the source.
Like any foil insulation with a fibrous core, traditional’ fibrous insulations carry the same risks. In fact, moisture can affect traditional insulations in an even greater way. They become compressed over time, lose their ability to insulate, and potentially develop problems like mould growth.
You can read more about moisture control in our blog Moisture Control – Why is it important?
Types of fibrous insulation
- Glass Wool (Fiberglass): Made from fine fibres of glass, fibreglass is one of the most common types of insulation. It’s lightweight, inexpensive, and effective but can irritate the skin and lungs during installation.
- Rock Wool (Mineral Wool): Made from rock, blast furnace slag, and other raw materials, which are melted and spun into fibres. It’s similar to fibreglass but has higher fire resistance and soundproofing qualities.
- Slag Wool: A type of mineral wool, slag wool is made primarily from iron ore blast furnace slag. It has properties similar to rock wool and is often used in similar applications.
- Cellulose: Made from recycled paper products, primarily newsprint, and treated with fire retardants. Cellulose insulation is environmentally friendly and provides good thermal and sound insulation. It’s commonly used in loose-fill or blown-in applications.
- Cotton (Denim): Recycled denim or other cotton textiles can be used for insulation. This type of insulation is environmentally friendly, does not irritate the skin or respiratory system, and provides good thermal and acoustic insulation.
- Sheep Wool: Natural sheep wool is an effective insulator and can absorb and release moisture without losing its thermal properties. It’s environmentally friendly and non-irritating but can be more expensive than synthetic options.
- Hemp Insulation: Made from the fibres of the hemp plant, it’s a natural, biodegradable option that offers good thermal and acoustic insulation properties.
- Wood Fiber: Wood fibre insulation is another eco-friendly option that provides good thermal insulation and breathability.
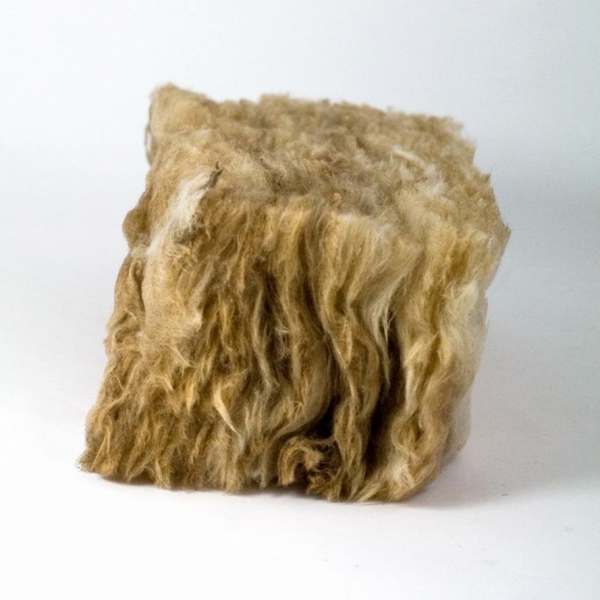
Rigid Foam (Board) Insulation
Rigid foam insulation, also known as foam board or insulating board, is a type of insulation material that comes in large panels of varying thicknesses. It’s made from various materials, such as polystyrene, polyisocyanurate (polyiso), and polyurethane.
It has a high R-value and is good at providing resistance to heat flow due to its closed-cell structure and its poor heat conductor traits. It’s also moisture-resistant and less prone to settling or sagging than fibrous insulation.
But they are expensive, have a significant environmental impact, can be highly flammable, have to be cut to fit, which can be difficult, create a lot of waste, and are bulky and inflexible, making them a nightmare to transport and store.
An Environmental Impact Note – In recent years, there has been worldwide criticism of the environmental impact of these types of insulation. Although designed to last 20+ years, once they come to the end of their life cycle, many rigid foams cannot be recycled, incinerated, or put into landfills. The waste needs to be kept dry and stored above ground. This will become a massive environmental issue over the next 20+ years, and reports of these products being cleaned out of our oceans and off our beaches are increasing.
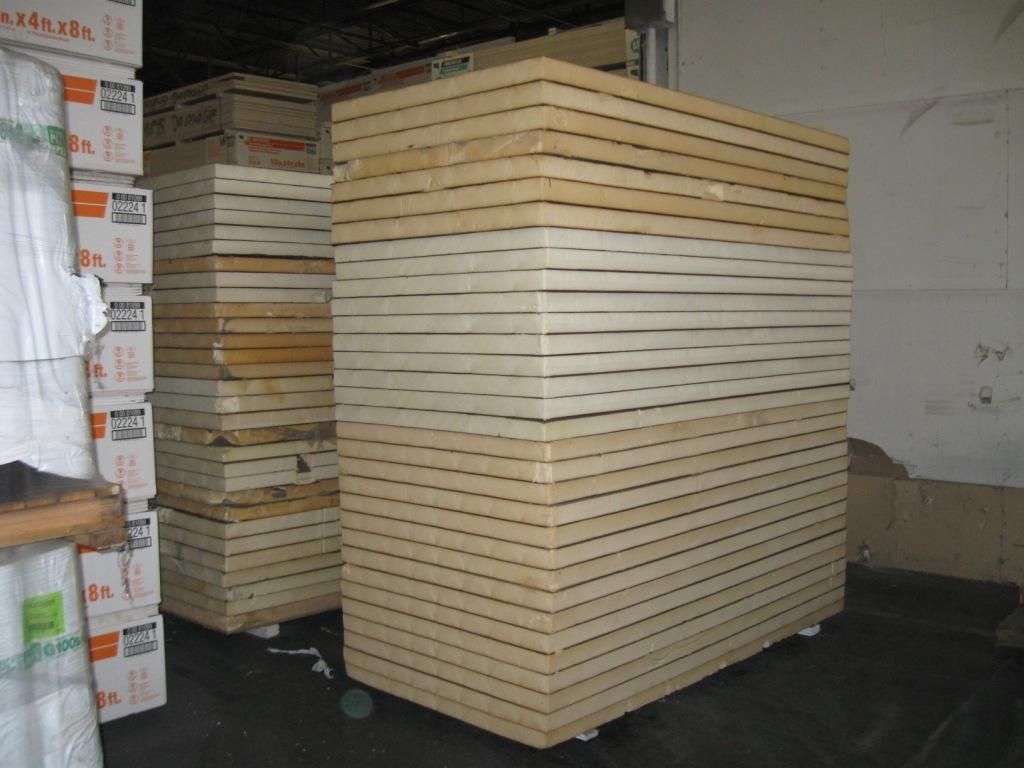
Low-E Insulation is different!
Low-E is not a multi-foil insulation, and it does not have any of these multi-foil drawbacks!
We pride ourselves on having one of the best fire ratings on the market. We achieved a Class 1 (BS 476) and have performed fire tests worldwide to the strictest standards. ASTM E84 and E603-77, AS NZS 1530.3
If you have read our blog – How does Low-E Insulation work? You will understand how foil insulation works and that surface material is the most essential part of reflective insulation.
The core is supplementary. So, if the surface works, why would you manufacture a product thicker than it needs to be?
You would be much better off using thinner foil insulation and thicker secondary insulation designed to be bulky and address the issues that bulk insulation needs to address.
It would also be quicker and cheaper to install!
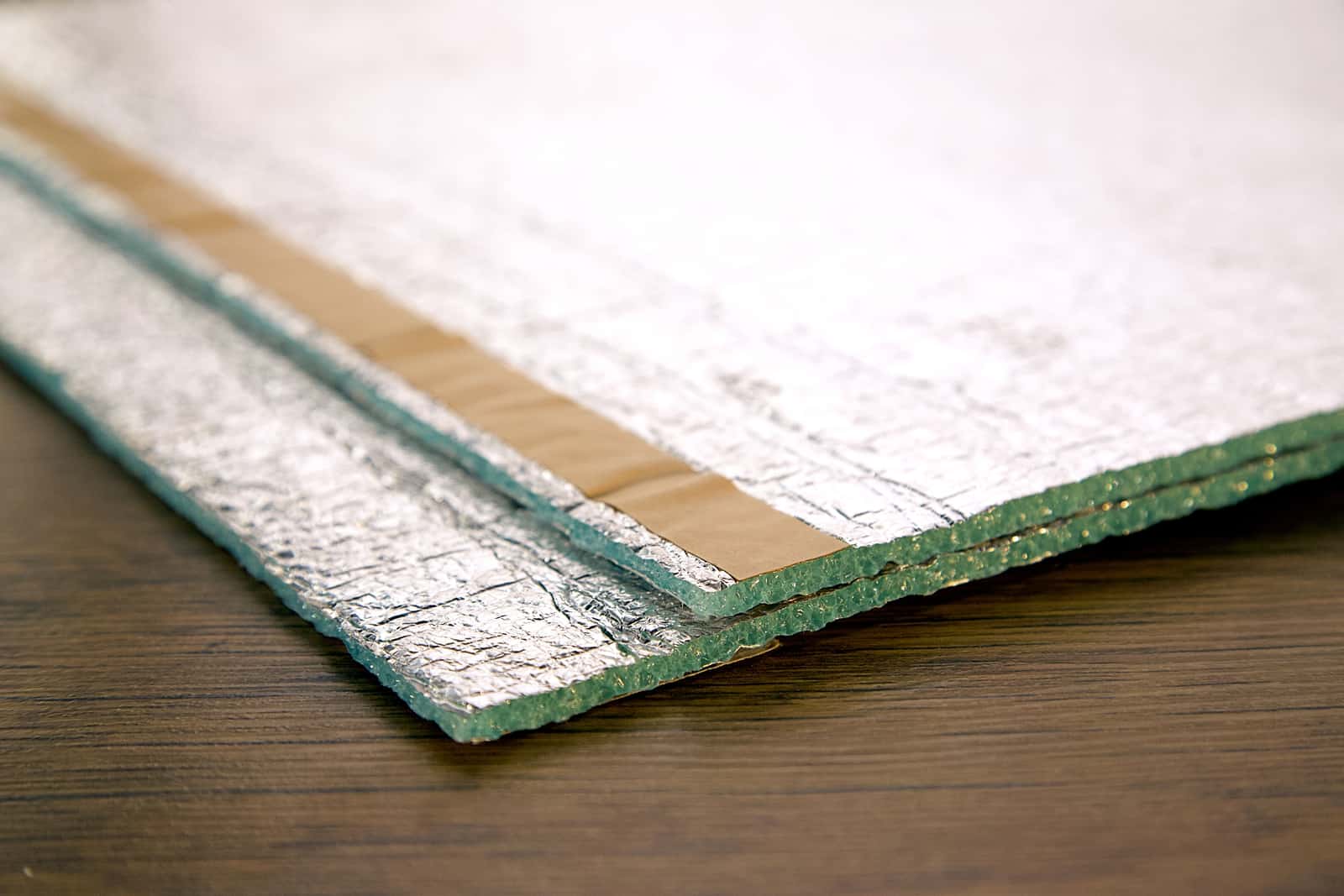
A Modern Solution – “People don’t understand, it doesn’t just save space in the building. We can design thinner wall and roof profiles, this means we can use smaller timbers, shorter nails and screws. The knock-on effect of utilising Low-E Insulation in buildings is huge”
– Anthony Brown – Director at Dwell Design Architects
Low-E Insulation
Low-E Insulation is arguably one of the best-performing insulations on the market. It has substantial environmental benefits over other insulation materials with the added advantage of occupying less space. Low-E is only 5.5mm thick. Occupying less space results in more internal floor space, but Low-E benefits more than just the finished building.
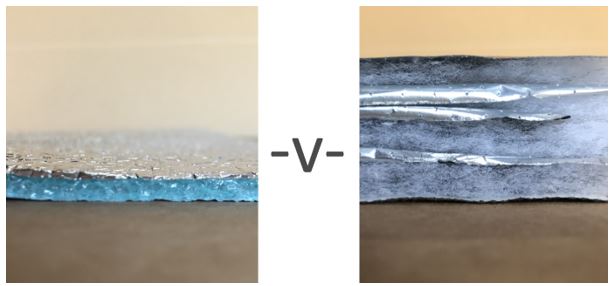
Transport and Storage
Using Low-E Insulation means there is much less material to transport on the roads and less material for the builder’s merchants to handle and deliver to and on-site. It reduces installation time and labour costs. The impact is massive.
Air Quality
‘Traditional’ insulations can hurt indoor air quality due to airborne fibres that can stick to your skin or get in your eyes; some are even classed as carcinogens and are produced using toxic blowing agents.
When using such traditional materials, it is always a good idea to combine a barrier material such as Low-E, which can prolong the life expectancy of an insulation system and stop airborne fibre and gases from entering internal spaces. It will also work to prevent the penetration of dust, pollen and other such allergens, making it ideally suited for use in homes, offices, schools and other health-sensitive applications.
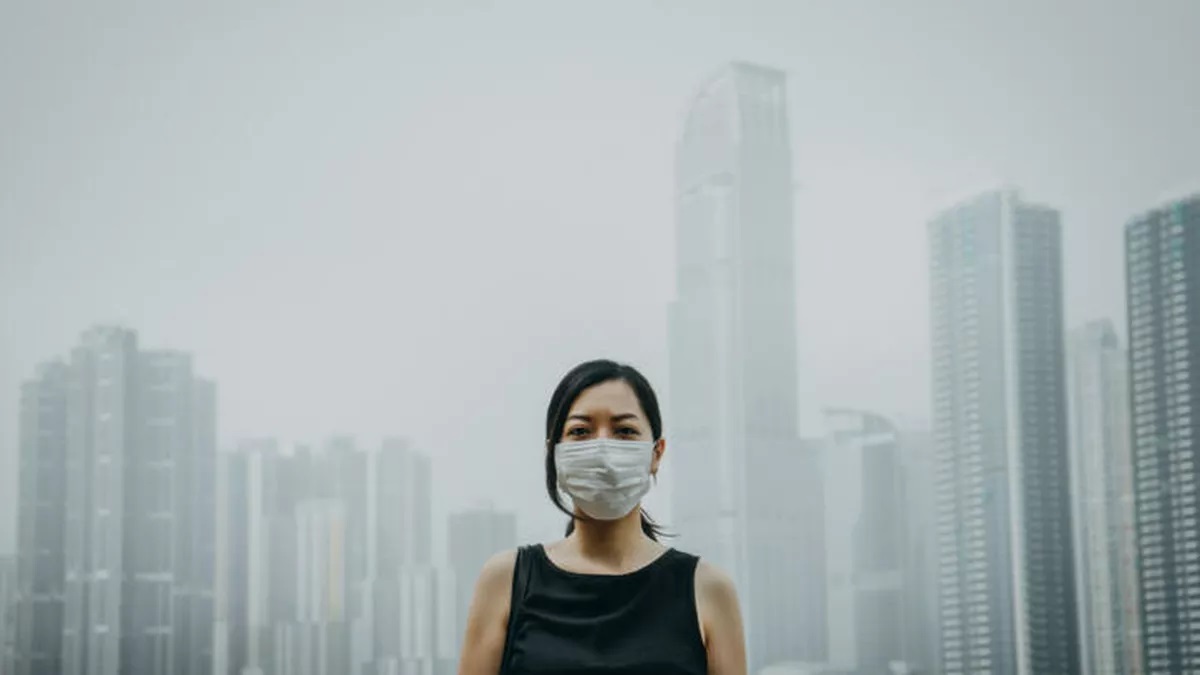
Combination Systems
Using Low-E Insulation as part of a combination system alongside fibrous insulation protects from absorption, prolonging the life of the insulation system.
Modern design and modern buildings require modern thinking. Using a combination of materials designed to address specific issues should be the best practice and the goal of all holistic designers and thinkers.
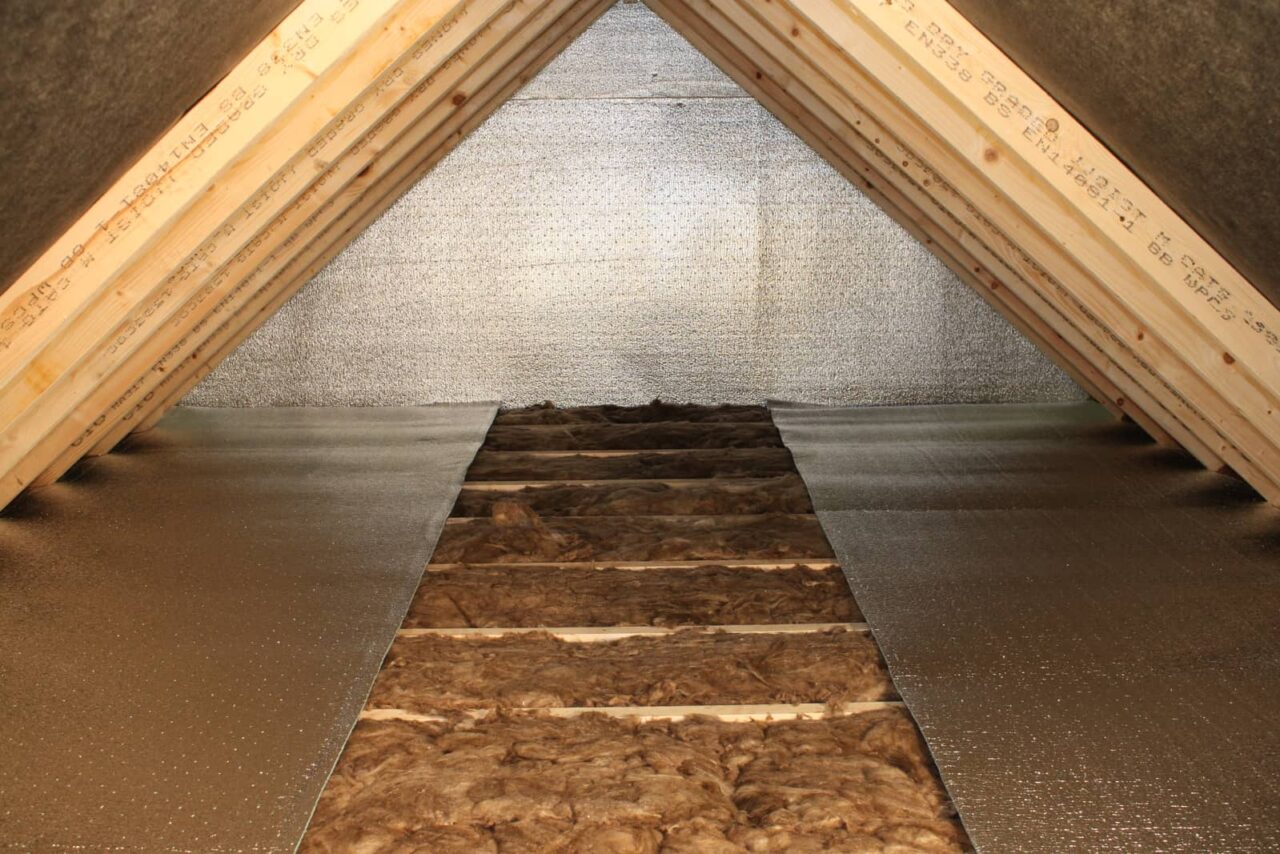
Recent Comments