MMC Building Systems
We get asked all the time about using Low-E Insulation with MMC Building Systems. Low-E insulation has never been specified as a stand alone product. Low-E performs a role within a building structure.
It is a vital and extremely functional role but Low-E is just part of a system within the building. A lot of companies when they design or produce new products focus on trying to take over an entire section of the market rather than simply promoting their product as a solution to a problem.
We have seen this first hand will Multi-foil insulations. New multi-foil insulations come to the market all the time adding more and more layers to try to increase the efficiency of their products. The idea is clearly to try and replace traditional insulation materials but these multi-foil products have become so thick they just don’t make sense.
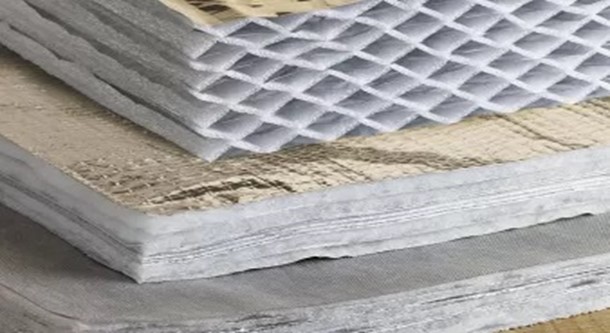
Why use a 70mm thick foil insulation that is more expensive, isn’t as thermal efficient and doesn’t have as good a fire rating, when you could use a system of traditional rockwool alongside a thin layer of Low-E?
As we have always said, foil Insulation has a vital role in construction, it acts as a vapour control layer, air infiltration barrier and it reflects radiant heat. These are roles required in modern construction that traditional insulation do not address.
In the case of Low-E Insulation it also will not absorb moisture, will not off gas, will not delaminate and because it is not a plastic Mylar and there are no glues used in production, it will not contribute to smoke or flame development.
There are new MMC Building Systems coming on the market every few months and having been a new comer to an established market over 30 years ago, we understand what these companies are up against. This blog is about different MMC building systems and the suitability of Low-E to be used alongside them.
ICF Construction
ICF stands for Insulated Concrete Form, but you should really think of these as reinforced Concrete (RC) Structures with insulation built in. They are extremely thermal efficient because they create an uninte
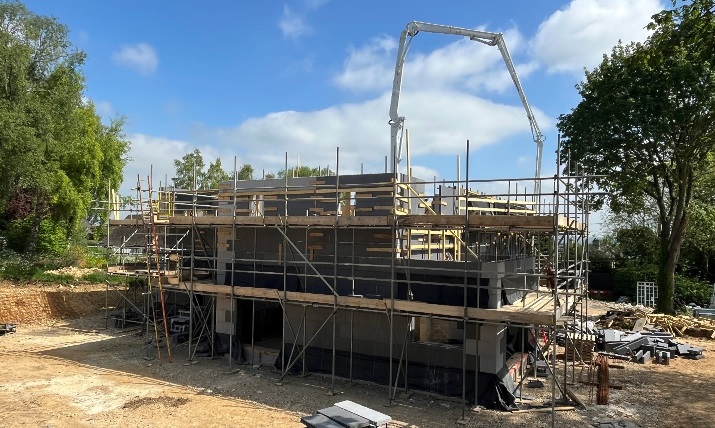
Traditionally built methods are designed as an internal leaf (usually blockwork) and an external leaf (usually brickwork) with a layer of insulation internally. The problem with this is that the brick and block and usually tied together using steel wall ties.
These conduct heat from the internal side to the external side. If you want to know what effect that has on the wall, here is an example that the difference between a wall with and without wall ties (but you can’t build a wall without wall ties)
100mm Brick – 120mm PIR Insulation – 100mm block (without ties) – 0.18 W/(m2K)
100mm Brick – 120mm PIR Insulation – 100mm block (with ties) – 0.24 W/(m2K)
PIR insulation (0.022 W/mK) – 2.5 (vertical twist galvanised steel) wall ties per m2
You can clearly see the effect that wall ties have on a structure. A traditionally built wall would need to be 12% thicker (377mm thick, instead of 337mm thick) just to counteract the effect of wall ties.
ICF construction eliminates the use of traditional wall ties. The ICF block usually consist of (the better ones do) a structural plastic web. The plastic web is more thermally efficient than the concrete core so it doesn’t contribute to thermal bridging. The layer of insulation on either side is usually made of EPS and can range in thickness to meet required U-values.
What I really like about ICF is, at the end of use (even if it is 100+ years) the building can be demolished and crushed. The concrete can be reused, the plastic webs can easily be recycled and so can the EPS.
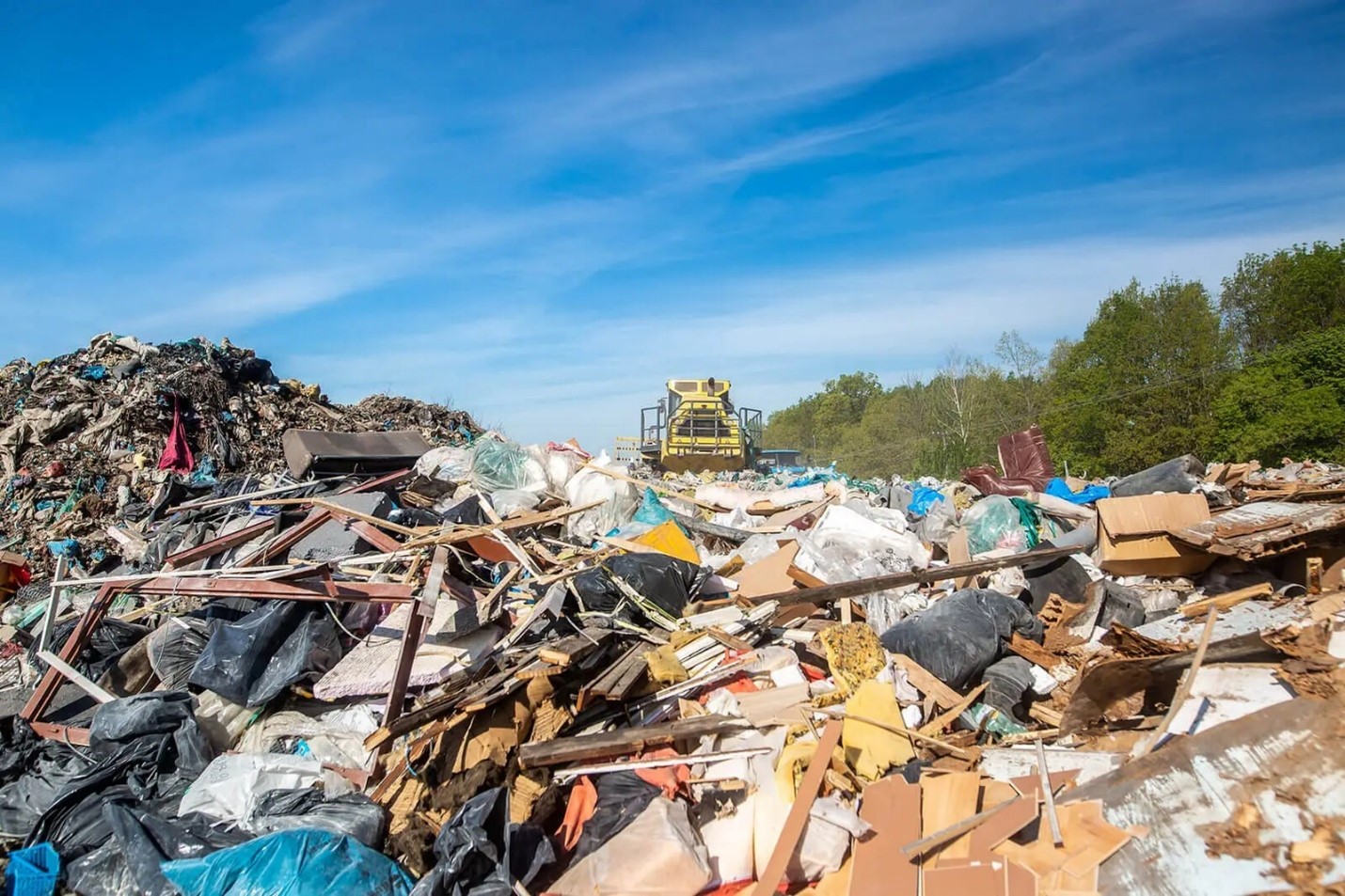
This is not the same as PIR which cannot be recycled and cannot be put into landfill because it leaches chemicals into the ground. It needs to be dry stored above ground (which never happens).
There are two things about ICF that are very progressive.
The finish on ICF is usually render or brick or stone slips.
Some people in the industry do not like slips because they are not traditional. But there are a few things to consider here. The UK has a housing shortage. We need more houses. Bricks are getting more and more expensive because we cannot manufacture enough of them and we are now importing more than 500 million bricks a year which is also coming at a huge Carbon cost. If the UK more widely adopted the use of brick slips we could bring down the cost of building.
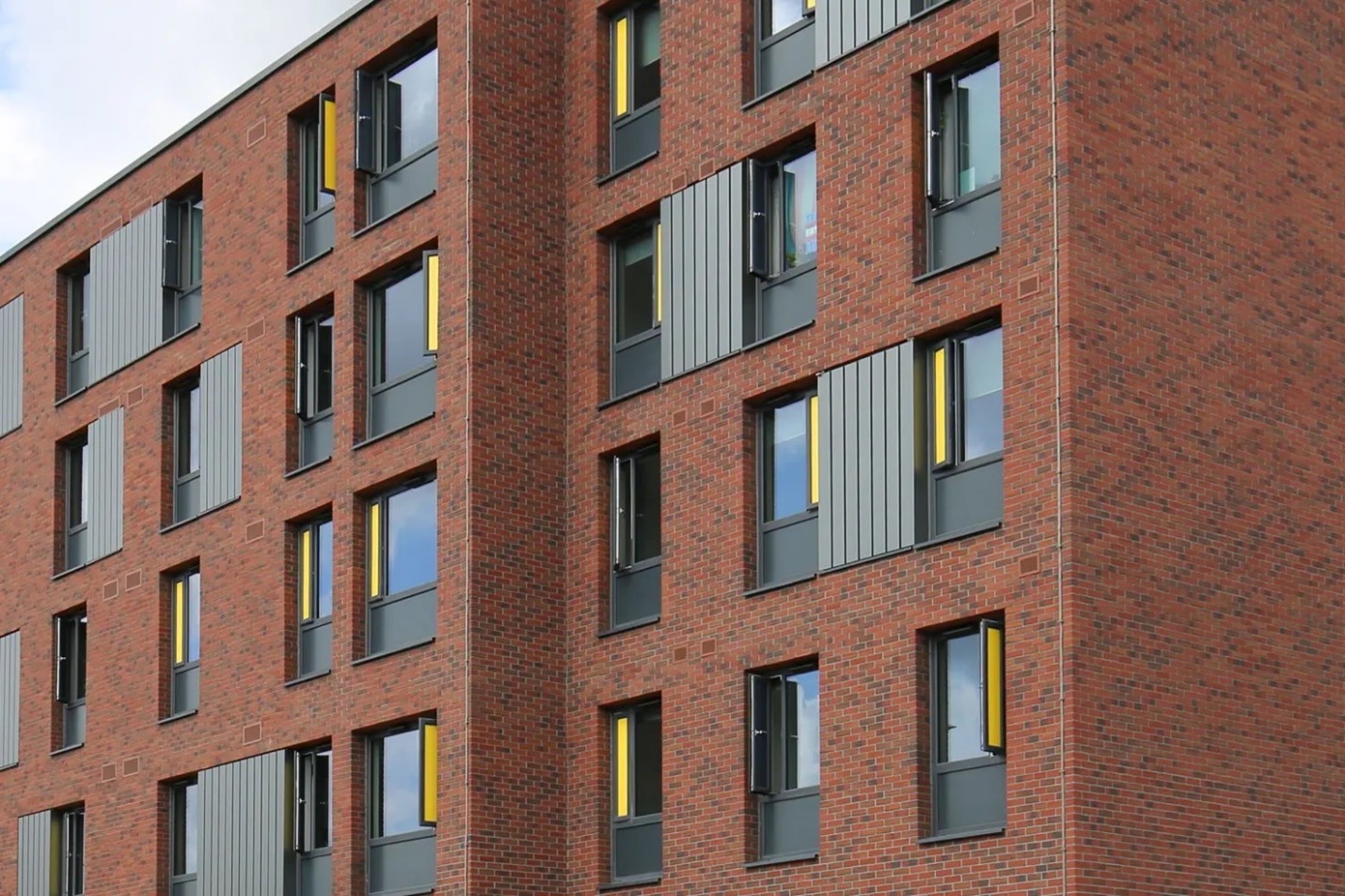
If architects got behind the use of slips and render we could start to design more attractive, well built houses and structures that reduce the need for importations, and more importantly can be built quicker. It is also worth pointing out that ICF houses need to meet the same standards as traditional buildings with regard to insulation standards, sound transmission, fire spread and impact resistance.
The other thing about ICF is that it needs to be installed by a trained person.
One of the issues we have had in the insulation industry is the lack of training required to install insulation and how badly installed a lot of insulation is.
The foil insulation manufacturers have been pointing this out for years. Foil insulation is very easy to install. And Low-E Insulation, because it doesn’t have layers, can easily be inspected for damage of tampering. Whereas, we have heard horror stories where installers separate layers of foil insulation or fibrous insulation to ‘make it go further’ reducing the overall performance of a building. And PIR insulation is supposed to be foamed, jointed and taped together but that rarely happens on site.
ICF needs to be installed by a trained person and in the case of ICF-Structure.co.uk they monitor their installers on every project through the use of inspection records carried out on site using an app on the installers phone.
We have worked with many contractors over the years and if these standards can be kept, it will be a very progressive and very welcome step forward for the entire industry.
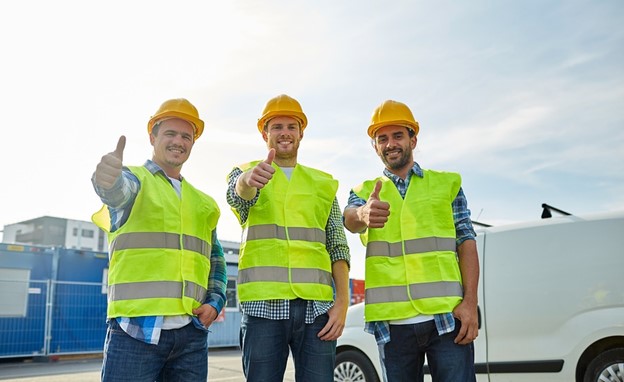
.So where does Low-E fit in here? While ICF is a very good product, again it does not reflect radiant heat. In a world where global warming is getting worse (all solar gain is radiant heat) the use of a radiant barrier is more relevant than ever. Low-E has been used to line the internal walls of ICF houses to increase efficiency and provide a radiant barrier. It is also widely used in the roofing of ICF houses where it can be installed along side, EPS, PIR or a fibrous Rockwool type product.
A final note on ICF is that it requires smaller install teams. Smaller teams means easier management and accountability. It means less accidents on site, it means less people on the roads driving to and from construction sites and it means faster building. We’ll have to watch this space but I for one am excited by this relatively new MMC building system
Timber Frame Construction
We regularly get asked about using Low-E Insulation in Timber Frame Buildings. Timber Frame is the old kid on the block when it comes to talking about MMC Building systems and Low-E Insulation has been widely adopted across the industry but timber frame construction itself has mixed success across a number of markets.
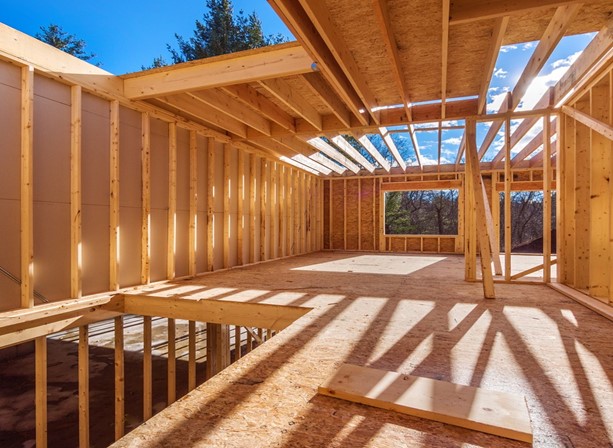
Timber frame building never really took off in the UK the way people expected, or some people hoped. There are a few reasons for this, but my feeling is that it was considered a European style of construction and deemed unsuitable for the English climate. Yet, timber frame has become very popular in Scotland where timber frame now accounts for over 85% of new build construction.
In Ireland, timber frame accounts for 15% of new builds (93% private housing and 7% of social housing). And in England it accounts for 23% of new builds. So perhaps the lack of uptake and reluctance is down to traditional methods and lack of progression in the construction industry.
Timber Frame houses are quiet, warm, cost effective and robust. While timber frame is incredibly fast to erect there can be long lead times for production.
Over the years we have supplied Low-E to a number of timber frame manufacturers and construction companies in the UK, Europe and across the USA who have been looking to improve the thermal performance of timber frame buildings and/or reduce the thickness of the wall profiles.
Low-E can be used in the walls, roof and floors of timber frame buildings as a VCL and airtight membrane while our PERF products, which are classed as breathable, can be used externally on roofs or walls as house wrap type products.
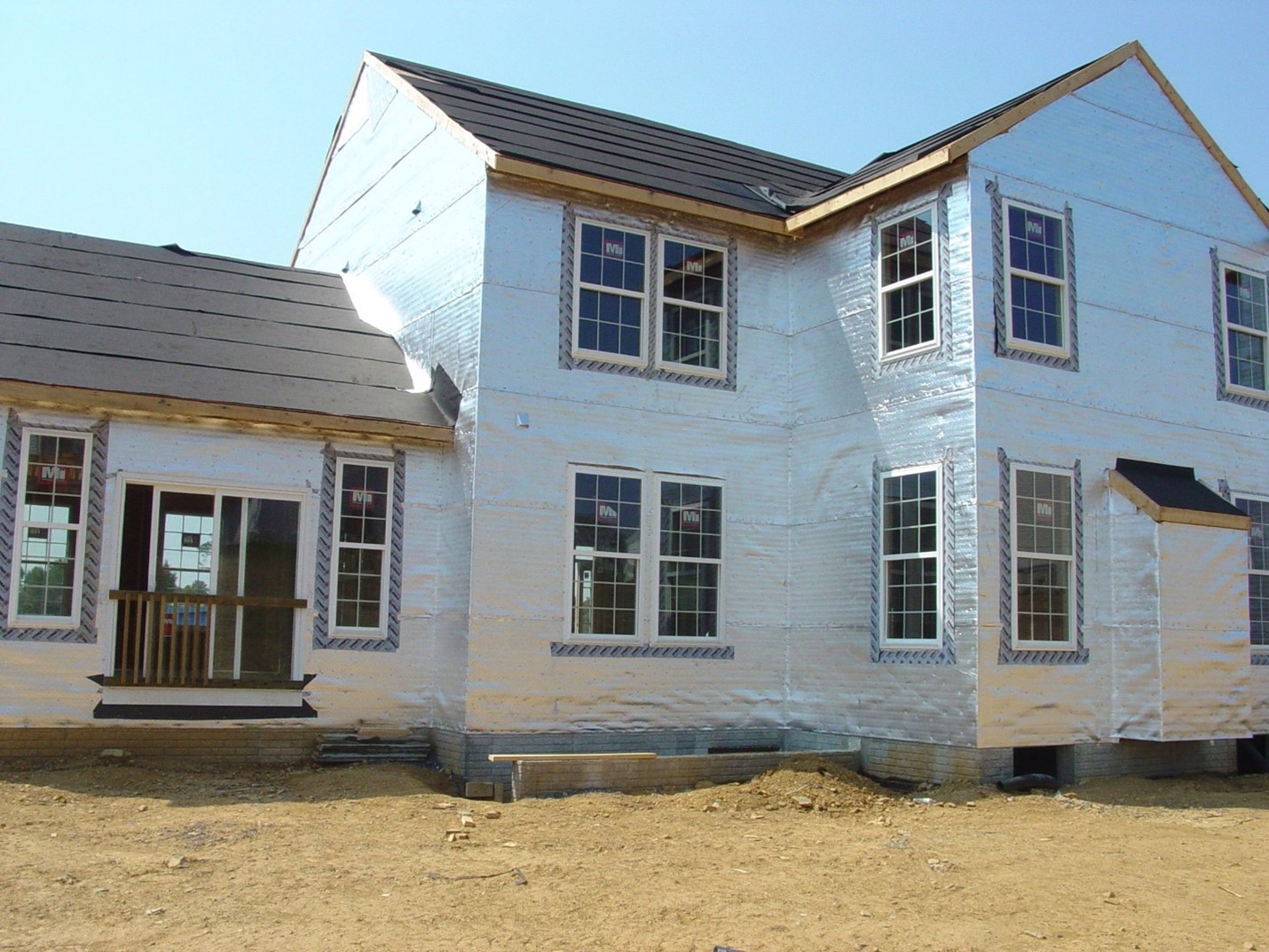
One of the drawbacks of off-site timber frame construction are the limitations on changes or delays caused by mistakes on site, which don’t happen on architectural drawings, but do happen in real world construction.
There is one company we have been working with that really are in the class of MMC when it comes to timber frame. They have a very interesting take on timber frame construction and are doing things a little differently.
Open Wall Off-Site have designed a timber frame panel that is compact and easy to handle. Best of all it is manufactured in a standard size panel which is fixed together on-site to build wall sections to the required size. This means they can mass produce panels and assemble them on site without any of the lead-in time required by bigger timber frame companies. This gives you the best of both worlds. The thermal performance and efficiency of timber frame building with the adaptability of on-site construction.
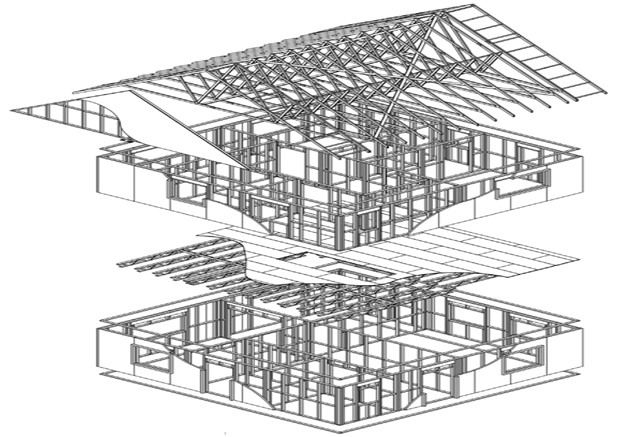
The unique design of Open Wall which integrates a Low-E VCL means their timber frame has a thinner profile than a standard timber frame wall. They are airtight, thermally efficient, easy to handle and quick to assemble.
Timber frame has a vital role in the delivery of new houses. In my opinion, timber frame doesn’t have enough market share but perhaps this new way of thinking about and delivering timber frame construction is what the UK has been waiting for. Let’s watch with interest how things progress for Open Wall Off-site.
Light Gauge Steel Frame (LGS) Construction
Steel Frame building is very similar to Timber Frame but is gaining in popularity faster in England than timber frame did. While timber frame buildings need to conform to the same standards as traditional buildings and steel frame, there is a perception that steel frame buildings are more durable and long lasting than timber frame. Another main driver, in my opinion, is that steel frames cannot absorb moisture and are non-combustible.
3D Printing
This is a completely new and radical idea for construction with very few active projects but is an interesting concept. I have been talking to installers and construction company regarding a couple of live project. My interest, for obvious reasons, is in how the insulation will be applied to these structures. And while they appear on paper to be more consistent and less disreputable by weather, I will be very interested to see if there are any real world financial saving or time benefit to the overall construction process.
Stay tuned…
Recent Comments